Także budynki pozbawione piwnic uległy pewnej modernizacji. Jeszcze pół wieku temu, w przypadku realizacji budynku niepodpiwniczonego, podłogi pomieszczeń parteru wykonywano na legarach drewnianych, opieranych pośrednio na murowanych z cegły słupkach posadowionych na gruncie.
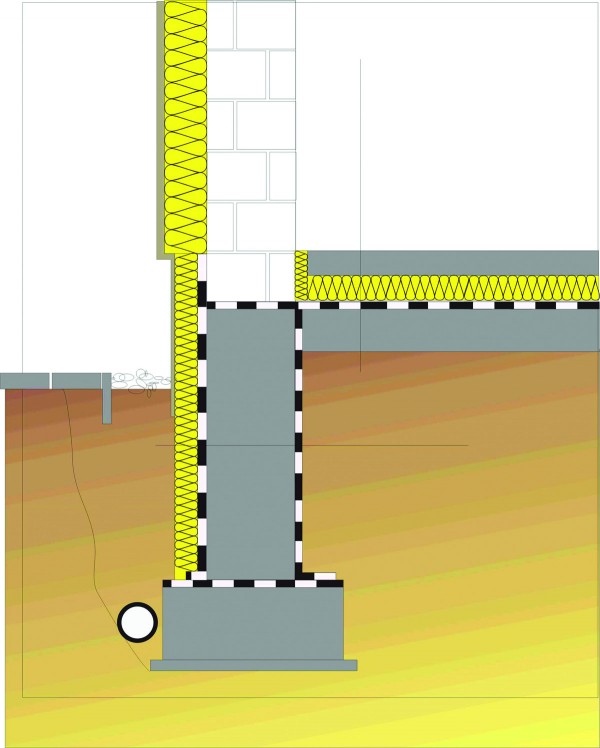
Tradycyjne konstrukcje podłogi w budynku pozbawionym piwnicy stanowiło w rzeczywistości wariant uproszczonego i posiadającego zminimalizowane rozpiętości stropu drewnianego. Niestety takie rozwiązanie posiadało liczne wady. Oprócz niskiej izolacyjności termicznej (podłogi wentylowane rzadko ocieplano od strony gruntu), więc zimno wiało przez szczeliny miedzy deskami, problem stanowiły przedostające się do mieszkań owady i gryzonie. Zwykle podczas użytkowania zdesperowani mieszkańcy zatykali, umieszczone w murach przyziemia otwory wentylacyjne. Konsekwencją było gromadzenie się w przestrzeni podpodłogowej wilgoci, co z kolei prowadziło to do przyspieszonego rozwoju mikroorganizmów niszczących drewno i w konsekwencji awarii podłogi i jej elementów konstrukcyjnych.
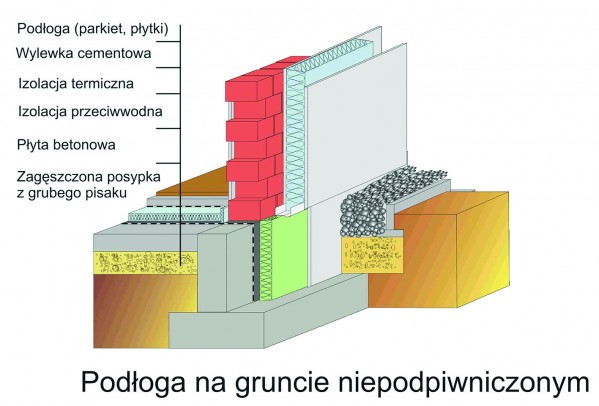
Obecnie stosowane rozwiązanie polegające na bezpośrednim ułożeniu podłogi na gruncie pozbawione są wielu wad wcześniejszych rozwiązań. Dlatego stały się powszechnie stosowane w budynkach mieszkalnych nie posiadających piwnic. Dostępne obecnie materiały i technologie powodują, że wielu inwestorom takie rozwiązanie wydaje się proste do wykonania przystępują samodzielnie, popełniając przy okazji liczne błędy.
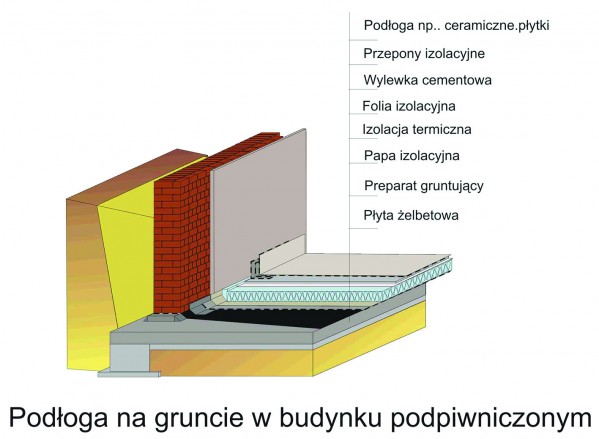
Podstawowe rozwiązanie podłogi wykonywanej na gruncie składa się z pięciu warstw.
Podsypka- przygotowanie podłoża
Przygotowanie tej warstwy należy rozpocząć od ułożenia przy ścianie izolacji termicznej. Oczywiście w przypadku, kiedy decydujemy się na izolacje układana pionowo, przylegającą do wewnętrznej ściany fundamentowej. W przypadku wyboru izolacji w układzie poziomym , jej wykonanie będzie jednym z kolejnych etapów robót. Możemy w takim razie rozpocząć przygotowanie podłoża. Zasadnicze czynności to, usunięcie warstwy ziemi ze elementami organicznymi z przestrzeni miedzy ścianami fundamentowymi. Usuwamy warstwę takiej grubości, aby pozostał w polach roboczych jedynie czysty piasek. Następnie należy uzupełnić ilość podsypki piaskowej przez rozściełanie warstw piasku o grubości ok. 15-20 cm i zagęszczanie ich metodą mechaniczną . Pamiętajmy, aby przed przystąpieniem do ubijania warstwę piasku zrosić wodą. Podobnie postępujemy układając kolejne warstwy , aż do poziomu górnej krawędzi ścian fundamentowych „-” ok. 15 cm.W celu uzyskania stabilniejszego podłoża można ostatnią warstwę piasku przemieszać z cementem , tworząc tzw. chudy beton. Po równomiernym rozściełaniu mieszaniny, należy ubić ją mechanicznie i dosyć intensywnie zrosić wodą. Układanie kolejnej warstwy można rozpocząć po okresie 2-3 dni.
Podkład betonowy
Jego zasadniczym zadaniem jest zapewnienia stabilności konstrukcyjnej podłogi oraz równomierne rozkładanie obciążeń statycznych, także tych z obciążenia ścianami działowymi. Podkład betonowy układa się metodą „na mokro” na zagęszczonym podkładzie. Podczas wykonywania tego elementu konieczne jest stosowanie betonu o konsystencji gęstoplastycznej. Nadmiar wody w mieszance, stanowi jedną z najczęściej występujących przyczyn wadliwego wykonania podkładów. Z jednej strony zawyżenie ilości wody zarobowej prowadzi do obniżenia rzeczywistej wytrzymałości betonu w stosunku do wytrzymałości projektowanej. W praktyce, wykonawcy usprawiedliwiają dodawanie wody w nadmiarze, rzekomą poprawą „rozlewności” lub urabialności mieszanki betonowej i co za tym idzie ułatwieniem rozściełania warstwy betonu. Koniecznie należy jednak pamiętać, że beton stosowany do wykonania podkładu powinien być przygotowany w konsystencji gęstoplastycznej. W prawdzie układanie betonu o konsystencji mocno porównywanej do mokrego piasku, jest trudniejsze niż rzadkiej mieszanki, ale korzyści są niewspółmiernie większe. Dzięki temu ograniczeniu ulega odebranie wody zarobowej do podłoża, łatwiejszy jest proces zagęszczania mechanicznego (ubijania betonu) oraz łatwiej jest wykonać w sposób prawidłowy zatarcie powierzchni podkładu „na ostro”. Po zakończeniu wiązania nie wystąpi także nadmierny skurcz podkładu. Koniecznie należy chronić ułożony podkład przed przedwczesnym osuszeniem np. w efekcie bezpośredniego działania wiatru lub promieni słonecznych. Zatarty podkład należy pielęgnować i regularnie zraszać wodą, w celu wydłużenia procesów hydratacji spoiwa cementowego.W przypadku wykonywania podłoży, na których nie zostaną posadowione ścianki działowe, dopuszcza się wykonanie podkładu jedynie z zastosowaniem betonu chudego o grubości ok. 15cm.
Warstwa izolacji przeciwwilgociowa
Na związanym podkładzie konieczne jest wykonanie warstwy zapewniającej ochronę podsadzki przed podciąganiem kapilarnym wilgoci gruntowej. Izolację przeciwwilgociową można wykonać zarówno z zastosowaniem tradycyjnych pap bitumicznych zgrzewanych lub łączonych na zakład metodą klejenia lepikiem albo nowszymi metodami zakładającymi wykorzystania folii PE lub PP. Folie powinny być na stykach klejone za pomocą specjalnych taśm, a zakłady sąsiednich pasów nie mogą być mniejsze niż 10 cm. Dla zapewnienia ciągłości membrany izolacyjnej konieczne jest wykonanie szczelnego połączenia między jej elementami, a izolacją poziomą murów (ścian fundamentowych). W przypadku podkładów wykonanych z betonu zwykłego, możliwe jest wykonanie izolacji przeciwwilgociowej techniką malarską z użyciem bezspoinowych materiałów polimerowo-bitumicznych. W takich przypadkach konieczne jest wcześniejsze zagruntowanie podłoża preparatem ograniczającym nasiąkliwość betonu i zapewniającym poprawę przyczepności masy izolacyjnej. Izolacje bezspoinowe należy wykonywać przez nałożenie dwóch lub więcej warstwa preparatu dostarczonego w stanie gotowym do aplikacji. Także izolacje bezspoinowe powinny zostać połączone za pośrednictwem specjalnych taśm z izolacją poziomą i pionową ścian fundamentowych, celem zapewnienia ciągłości warstw.Zależnie od rodzaju materiału użytego do wykonania izolacji przeciwwilgociowej zaleca się stosowanie odpowiednio dobranej izolacji termicznej.
REKLAMA:
Warstwa izolacji termicznej
Do jej wykonania konieczne jest zastosowanie materiału o szczególnych właściwościach. Z jednej strony powinien on zapewniać możliwie najlepszą izolacyjność termiczną, czyli posiadać w swoim wnętrzu duża ilość powietrza, z drugiej strony musi cechować się znaczną wytrzymałością mechaniczną i nie zmieniać swoich właściwości termoizolacyjnych w skutek nacisku wywołanego przez warstwę podkładu wyrównującego. Najpowszechniej stosowanym materiałem, spełniającym wymienione wcześniej wymagania jest polistyren spieniony(PS) czyli styropian o gęstości 20lub 30 kg/m 3 . Oprócz wymienionych cech warto dodać, że wykazuje on niską nasiąkliwość, nie ulega starzeniu i rozkładowi organicznemu. W praktyce ma jednak pewne ograniczenia. Otóż nie należy układać go na izolacjach przeciwwilgociowych wykonanych z zastosowaniem rozpuszczalnikowych preparatów polimerowo- bitumicznych (na preparatach wodorozcieńczalnych nie ma problemu). Istnieje bowiem niebezpieczeństwo, że opary rozpuszczalnika wypływające z masy izolacyjnej spowodują zniszczenia granulek styropianu. W przypadku układania na papach bitumicznych lub foliach polimerowych ograniczenia nie ma. Oprócz tego do zastosowania podłogowych zaleca się stosowanie wełny mineralnej, twardej. Oczywiście wełna mineralna posiada wiele zalet i jest równie doskonałym materiałem termoizolacyjnym, zapewniającym dużą izolacyjność termiczną (to znaczy zawierającego w swoich porach możliwie największą ilość powietrza). Posiada także konieczne do tego zadania parametry wytrzymałościowe. Jednak w opinii niektórych wykonawców i projektantów wątpliwości budzi jej dość wysoka nasiąkliwość. W przypadku zwyczajnego użytkowania pomieszczeń nie stanowi to problemu, jednak w razie zalania budynku np. w skutek awarii instalacji wodociągowej, usunięcie zgromadzonej w wełnie wilgoci może okazać się trudne. Dlatego, jeżeli decydujemy się na wykonanie termoizolacji z wełny mineralnej , konieczna jest dodatkowa warstwa izolacji przeciwwilgociowej (folii PE), oddzielająca materiał izolacyjny od podkładu wyrównującego.Najczęściej popełniane podczas wykonywania tych robót błędy to: układanie materiału termoizolacyjnego o zbyt niskiej gęstości i twardości oraz brak izolacji (właściwie dylatacji wykonanej z zastosowaniem materiału termoizolacyjnego) obwodowej przy ścianach pomieszczeń. Skutkiem obu zaniedbań może być pękanie warstwy wyrównawczej.
Wykonanie warstwy termoizolacyjnej powinno ograniczać straty ciepła z pomieszczeń ogrzewanych. Przyjmuje się, że grubość tej warstwy powinna wnosić ok. 10-12 cm. Jeśli izolację termiczną zabezpieczymy od góry warstwą folii, najlepiej z ekranem metalizowanym, to uzyskaliśmy podbudowę przygotowaną do wykonania ogrzewania podłogowego.
W każdym przypadku konieczne jest jednak wykonanie jeszcze jednej warstwy:
Warstwy wyrównawcze, warstwy dociskowe, jastrychy
Warstwa wyrównująca ma za zadanie stworzyć podłoże do wykonania posadzki w pomieszczeniu. Obecnie powszechnie stosowane są zarówno tradycyjne wylewki betonowe, jak i jastrychy samopoziomujące oparte o spoiwa cementowe oraz samopoziomujące podkłady anhydrytowe. Bez względu na stosowany materiał, zadanie podkładu jest takie samo. Stworzyć stabilny, poziome podłoże dla warstwy wykończeniowej (płytek, parkietu, wykładzin rulonowych). Podkłady samopoziomujące wymagają odrębnego potraktowania, dlatego jedynie sygnalizuję możliwość ich zastosowania.W przypadku wykonania jastrychu z betonu, konieczne jest zastosowanie się do kilku podstawowych wymogów. Przede wszystkim ważne jest, aby konsystencja użytego betonu była gęstoplastyczną. Przed przystąpieniem do układania warstwy niezbędne jest wyznaczenie poziomu górnej płaszczyzny jastrychu. Praktyka wskazuje, że łatwiej jest układać podkłady o większej grubości. Dlatego wydaje się, że w pełni uzasadnione jest wykonanie wylewki o grubości minimalnej ok. 4,0-4,5 cm. W prawdzie zużycie materiału wzrośnie, ale łatwiej będzie uzyskać poziomą i prawidłowo zatartą powierzchnię. Stanowią zasadniczy pod względem statycznym element układu. Warstwa dociskowa zapewnia nie tylko ochronę umieszczonych poniżej warstw izolujących, ale stanowi także podłoże do wykonania elementów posadzek.
Wykonaną warstwę betonową należy pielęgnować, przez kilkudniowe zraszanie wodą. Pozwoli to na przedłużenie okresu hydratacji spoiwa cementowego i uzyskanie wysokiej wytrzymałości. W przypadku wykonywania jastrychu, jako płyty grzejnej jej grubość jest zdecydowanie większa. Przy ogrzewaniu wodnym wynosi ok. 6,0-8,0 cm.
Częstą przyczyną awarii warstwy wyrównującej jest brak lub wadliwe wykonanie dylatacji. Oprócz przygotowania przed wykonaniem wylewki dylatacji obwodowej , konieczne jest także nacięcie szczelin dylatacyjnych już po częściowym związaniu spoiwa w wylewce. Należy koniecznie pamiętać o zdylatowaniu narożników wystających oraz miejsc przewężenia jastrychu np. przy otworach drzwiowych. Dylatację wykonuje się przez nacięcie podkładu tarczą do kamienia na 2/3 grubości warstwy.
Od jastrychu wymaga się, żeby został wykonany idealnie poziomo. Jednak w praktyce spełnienie tego wymogu jest dosyć trudne. Dlatego producenci chemii budowlanej dostarczają średnio– i cienkowarstwowe „posadzki” samopoziomujące. Po zarobieniu wodą suchej mieszanki, możliwe jest wylanie warstwy o grubości 2-10(12) mm . Po wstępnym rozścieleniu masy i jej odpowietrzeniu, uzyskujemy gładkie, nie wymagające zacierania podłoże do układania posadzek drewnianych i drewnopochodnych lub wykładzin podłogowych.
Podłogi spoczywające bezpośrednio na gruncie spotykamy nie tylko w budynkach niepodpiwniczonych , ale także stanowią podłogi piwnic. Choć ich wykonanie nie należy do zadań szczególnie trudnych, ilość obserwowanych błędów i związanych z nimi awarii posadzek , wskazuje, że warto przypominać zasady ich wykonania nawet doświadczonym wykonawcom.
REKLAMA:
REKLAMA:
Źródło: Obud