Wśród szeregu produktów obecnych w ofercie RUBI® szczególną uwagę zwraca nowa generacja przecinarek elektrycznych do cięcia płytek ceramicznych (modele DS) oraz materiałów budowlanych (modele DX). Oba modele zawierają całkowicie nowe rozwiązania konstrukcyjne i materiałowe w stosunku do poprzedniej linii DS/DX.
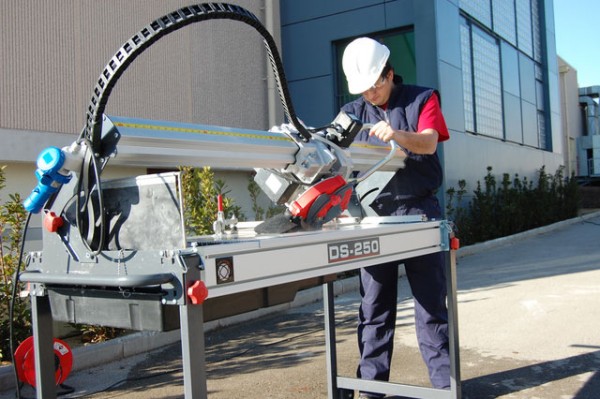
Podstawowe dane techniczne przecinarki DS-250/1000 podano poniżej:
- moc: 2,2 kW (opcjonalnie 3 kW);- prędkość bez obciążenia: 2800 obr/min;
- średnica tarczy: 250 mm (otwór wewnętrzny 25,4 m);
- maks. głębokość cięcia: 50 mm;
- maks. długość cięcia: 100 cm (opcjonalnie 130 / 150 cm);
- cięcie pod kątem: tak (płynna regulacja do 45o);
- masa: ok. 100 kg;
- wyposażenie: zestaw kluczy do odkręcania tarcz, regulacji maszyny, przymiar boczny, przymiar do cięć seryjnych, uchwyt do unieruchamiania płytek na blatach roboczych (w dłuższych wersjach listwa mocująca na całej długości blatów), obejmy do usztywnienia tarczy podczas cięcia pod kątem, końcówka kabla do podłączenia do maszyny, instrukcja obsługi;
- zastosowanie: cięcie płytek ceramicznych, gresowych i płyt kamiennych o dużych gabarytach pod kątem prostym i kątem 45o; możliwe inne wersje o większej długości (1300, 1500) oraz większej wysokości cięcia (DS-300).
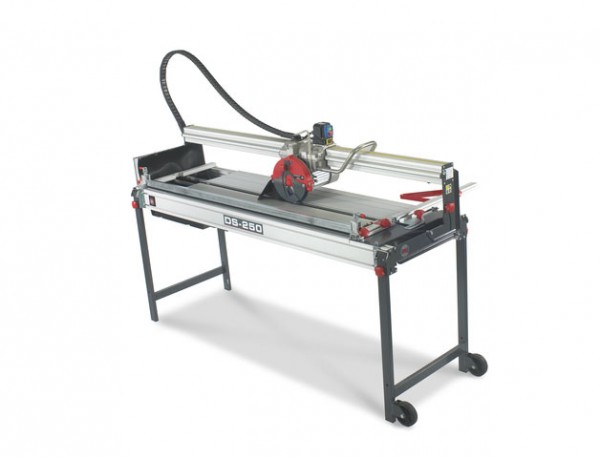
A więc, po kolei:
Na jakie parametry należy zwrócić uwagę podczas zakupu przecinarki (pilarki) do płytek?
Decydując o wyborze przecinarki elektrycznej do płytek ceramicznych, gresowych oraz płyt kamiennych należy zwrócić uwagę na kilka czynników. Jednym z nich jest gwarantowana przez maszynę długość cięcia, umożliwiająca obróbkę popularnych wymiarów płytek wzdłuż dłuższego boku, ale i po przekątnej (np. płytka o wymiarach 60x60 przecinana po przekątnej wymaga ok. 85-90 cm długości cięcia). Drugim istotnym parametrem jest głębokość cięcia określająca maksymalną grubość ciętego materiału. Jeżeli konstrukcja maszyny pozwala na zagłębianie tarczy, wówczas możliwe jest wykonywanie cięć podwójnych (czyli głębszych po odwróceniu materiału) oraz nacięć w środku płytki. Wykonawcy często zwracają uwagę na moc silnika i rzeczywiście - im większa moc, tym stabilniejsza jest praca, szczególnie w materiałach grubszych (powyżej 20 mm), jednak należy pamiętać, że o płynności cięcia decyduje przede wszystkim odpowiednio dobrana do danego materiału tarcza diamentowa. Decydując o wyborze przecinarki należy również zwrócić uwagę na jej konstrukcję zapewniającą wygodę i bezpieczeństwo użytkowania, a więc czy zapewniona jest stabilność podczas cięcia, czy jest możliwy łatwy demontaż nóg i stołu roboczego, a za tym sprawne umycie maszyny po zakończeniu prac oraz jej przewożenie, czy jest możliwe przeprowadzanie powtarzalnych regulacji, czy są dołączone przymiary i listwy mocujące płytkę na blatach. Przy wyborze przecinarki należy również pamiętać o planowanym miejscu wykonywania prac – czy są to remontowane mieszkania prywatne, do których bardziej nadaje się maszyna mniejsza, czy np. domy lub hale, w których łatwiej wygospodarować miejsce na maszynę o większych rozmiarach.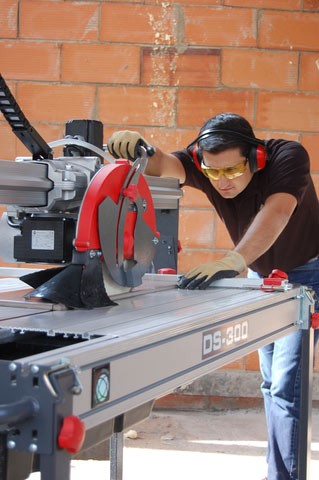
Jakie błędy są najczęściej popełniane podczas cięcia twardych lub grubych płytek np. w dwóch cięciach?
Najczęstsze błędy popełniane przez wykonawców podczas cięcia to stosowanie niewłaściwego rodzaju oraz modelu tarczy. Tarcza powinna być odpowiednio dobrana pod względem jakości oraz twardości obrzeża tnącego, które w ciętym materiale będzie powoli ulegało ścieraniu odsłaniając nowe ziarna diamentów. Przy cięciu materiałów o grubości większej niż 20-30 mm można zastosować tarczę typu turbo (obwód ciągły z nacięciami), która zapewnia szybsze cięcie oraz lepsze odprowadzanie urobku i chłodzenie. Kolejny częsty błąd to brak odpowiedniego chłodzenia tarczy. Strumień wody podawany przez pompę powinien być wystarczająco mocny, by nie tylko schłodzić ale również oczyścić tarczę z urobku. Ponadto prowadząc tarczę w ciętym materiale należy czynić to w sposób spokojny i jednostajny, bez gwałtownych szarpnięć. Zbyt szybkie cięcie może doprowadzić do skrzywienia toru cięcia, przegrzania lub nawet spalenia tarczy.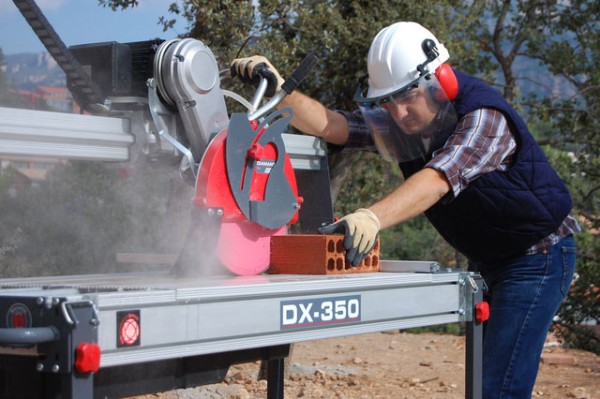
W jaki sposób należy dobrać prawidłowo tarcze dla materiałów o różnej twardości?
Przy wyborze tarczy należy sugerować się opisami zamieszczonymi przez producenta określającymi ich przeznaczenie. Odpowiednie dobranie tarczy diamentowej do konkretnego materiału istotnie wpływa na szybkość i jakość cięcia oraz żywotność tarczy. Segment diamentowy jest wykonany z mieszanki ziaren diamentu syntetycznego (o różnej wielkości i regularności kształtów), które „wtopione” są w korpus wykonany ze stali lub stopu metali lekkich. W zależności od wielkości i gęstości ułożenia ziaren diamentu, rodzaju spoiwa, kształtu obrzeża, tarcze diamentowe mają różne właściwości ścierne i w związku z tym są przeznaczone do różnych materiałów (np. jedne do miękkich płytek ceramicznych, inne do twardych gresowych, a jeszcze inne – do materiałów budowlanych). Bardzo częstym błędem jest stosowanie przez glazurników tarczy przeznaczonej do cięcia twardego gresu jako tarczy „najlepszej” do wszystkich materiałów. Tymczasem taka tarcza w materiale miękkim po pewnym czasie ulegnie stępieniu i mimo, że na pierwszy rzut oka widoczny będzie jeszcze segment tnący, to jednak na jego powierzchni nie będzie żadnych nowych ziaren diamentu umożliwiających dalsze cięcie. Jeśli glazurnik musi wykonać szereg cięć w różnych materiałach, wówczas dobrym rozwiązaniem może być tarcza uniwersalna, której dodatkowym plusem jest szybkie cięcie, natomiast minusem szybsze zużycie oraz możliwość lekkiego szarpania krawędzi cięcia. Najlepszym rozwiązaniem jest posiadanie co najmniej 2 lub 3 tarcz przeznaczonych do różnych materiałów i stosowanie za każdym razem tej odpowiedniej, co przełoży się na szybkość i jakość wykonania prac oraz żywotność tarcz. Należy także pamiętać, iż intensywne używanie tarczy do cięć ukośnych powoduje jej nierównomierne (jednostronne) zużycie, skutkiem czego może być utrudnione wykonywanie taką tarczą cięć prostych.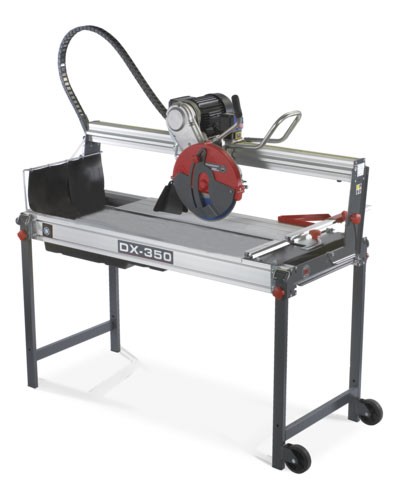
Na czym polega kalibracja maszyny do przecinania płytek ceramicznych i jak często należy ją wykonywać?
Jakość cięcia płytek ceramicznych zależy w dużej mierze od stosowanej tarczy, jednak równie ważnym elementem jest prawidłowe wyregulowanie samej przecinarki. Podczas podstawowego przeglądu przecinarki i ewentualnej kalibracji należy zwrócić uwagę na kilka elementów:1) czy nie ma luzów w systemie prowadzenia głowicy, ewentualnie należy je usunąć;
2) czy tarcza jest ustawiona idealnie równolegle w linii z prowadnicą, po której głowica jest przesuwana;
3) czy blaty robocze, na których leży płytka są idealnie płaskie i równoległe względem siebie;
4) czy jest zachowany kąt prosty pomiędzy płaszczyzną tarczy, a płaszczyzną stołu roboczego przy obydwóch ramionach maszyny;
5) czy jest zachowany kąt prosty pomiędzy planowaną linią cięcia, a ogranicznikiem głównym;
6) czy pompa wodna i rurki doprowadzające wodę do chłodzenia tarczy są drożne.
REKLAMA:
Kalibrację maszyny należy przeprowadzać, jeśli pojawiają się nieprawidłowości podczas cięcia. Jednak oprócz maszyny należy również skontrolować, czy tarcza jest odpowiednio dobrana i naostrzona oraz czy boki, kąty oraz płaszczyzny ciętych płytek są równe.
REKLAMA:
REKLAMA:
Źródło: Rubi